The Role of Change Management in Hazardous Substance Control
Control chemical hazards safely with effective change management. Discover key risks, practical steps, and NEBOSH’s role in strengthening workplace safety.
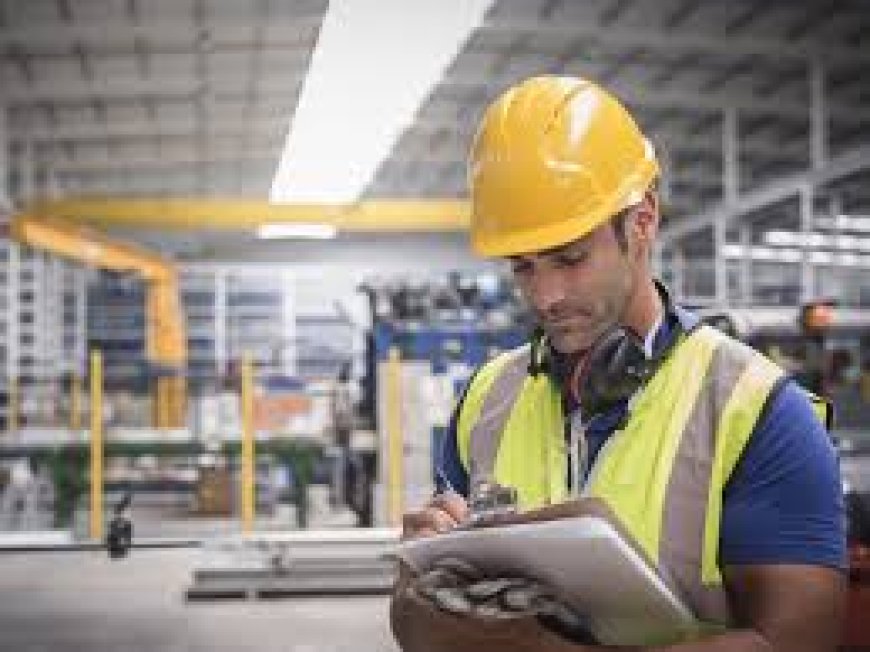
When it comes to workplace safety, few areas are as critical — and potentially dangerous — as the management of hazardous substances. From chemicals in manufacturing plants to cleaning agents in hospitals, even minor changes in how these materials are handled, stored, or used can introduce new risks. This is where change management becomes vital in hazardous substance control.
Without a clear, structured approach to managing changes in how hazardous substances are handled, companies risk accidents, chemical exposures, fires, and regulatory breaches. In this article, we’ll explore the importance of integrating change management into hazardous substance control, examine common hazards, share practical steps, and explain how professional safety qualifications can strengthen this process.
For those looking to deepen their expertise in workplace safety, investing in professional certifications like NEBOSH can make a significant difference. Understanding the NEBOSH Fee in your region is essential before committing to a course. In Pakistan, NEBOSH fees depend on the course type, level, and provider — but this investment offers long-term value in career growth and workplace safety leadership.
Why Change Management Matters in Hazardous Substance Control
Workplaces rarely stay the same. New materials are introduced, storage areas are reorganized, processes are revised, and personnel changes happen. Each of these adjustments, no matter how small, can affect the safe management of hazardous substances.
If these changes are made without properly assessing their impact on chemical safety, they can lead to:
-
Exposure to harmful vapors, dust, or liquids
-
Increased fire or explosion risks
-
Inadequate emergency response procedures
-
Incorrect personal protective equipment (PPE) for new hazards
-
Environmental contamination
This is why change management is a crucial part of any chemical hazard control program. It ensures that before any change is implemented, its safety implications are understood, controlled, and communicated to everyone involved.
Common Workplace Hazards During Hazardous Substance Changes
Even seemingly minor changes can increase risks dramatically. Some common hazards include:
-
Storing incompatible chemicals together after reorganizing a storeroom
-
Introducing a new cleaning chemical without updating Safety Data Sheets (SDS)
-
Switching suppliers or containers with different hazard classifications
-
Moving hazardous materials through public or poorly ventilated areas
-
Installing new machinery that uses or produces hazardous substances
Anecdote:
At a metal plating workshop, management switched to a new type of degreasing solvent. However, they neglected to conduct a change management review. The new solvent was highly flammable compared to the old one. A spark from nearby machinery ignited vapors, causing a fire that injured two workers. A proper change management process could have identified this risk and prevented the incident.
How Change Management Strengthens Hazardous Substance Control
A structured change management process acts like a safety net, catching hazards before they cause harm. It ensures that:
-
New risks are identified and assessed before changes happen
-
Controls are updated to address additional hazards
-
Employees receive updated training and instructions
-
Emergency plans are revised to match new conditions
-
Regulatory compliance is maintained
Step-by-Step Guide: Managing Changes in Hazardous Substance Control
To safely manage changes involving hazardous materials, follow this practical process:
Step 1: Identify the Change
Clearly define what is changing. This might be:
-
A new chemical or hazardous substance
-
New storage or handling methods
-
Changes to work areas, processes, or staff responsibilities
Step 2: Assess New and Existing Hazards
Use a formal risk assessment process to evaluate:
-
New hazards introduced by the change
-
Existing hazards made worse by the change
-
Who might be affected and how
Step 3: Implement New Control Measures
Based on your assessment, update:
-
Personal protective equipment (PPE) requirements
-
Ventilation systems
-
Emergency procedures and signage
-
Safe handling and storage instructions
-
Spill response plans
Anecdote:
A hospital housekeeping team introduced a new floor-cleaning chemical. By involving staff in a quick hazard assessment, they discovered the product produced harmful fumes when mixed with certain disinfectants already in use. The chemical supplier was consulted, and usage instructions were revised to prevent cross-contamination — all because change management principles were applied.
Step 4: Communicate Changes Clearly
Inform all employees and contractors who might be affected by the change. Use:
-
Toolbox talks
-
Safety briefings
-
Noticeboards
-
Emails or digital alerts
Ensure they understand new hazards, controls, and emergency actions.
Step 5: Provide Training
If the change involves new substances, PPE, procedures, or storage arrangements, deliver targeted training. Don’t assume people will pick up the changes on their own.
Step 6: Review and Monitor
After the change is made:
-
Observe for issues or near-misses
-
Gather feedback from staff
-
Adjust controls or procedures if necessary
-
Keep records for compliance and future audits
The Value of Professional Training in Hazardous Substance Control
Even experienced safety managers benefit from formal training when handling hazardous substances and managing changes effectively. One of the most recognized qualifications in this field is the NEBOSH certification.
Before enrolling, it’s a good idea to check NEBOSH Fee structures in your area. In Pakistan, these fees differ based on course type (like NEBOSH IGC or Diploma) and training providers. Though it requires an upfront investment, a NEBOSH certificate strengthens your ability to manage workplace hazards and builds confidence among your team and employers.
Ready to advance your safety career? Discover your options at the Best NEBOSH Institute in Pakistan and find a course that suits your safety management goals.
Additional Tips for Managing Hazardous Substance Changes
Involve Employees in Decision-Making
Workers often spot practical hazards managers overlook. Involve them in risk assessments and change planning sessions.
Update Safety Data Sheets (SDS)
Ensure all SDS documents reflect the latest products, substances, and procedures — and are easily accessible to staff.
Use Compatible Storage and Containers
When switching chemicals, confirm that storage areas, containers, and labels meet safety standards for the new substances.
Adjust Emergency Plans
Review evacuation routes, spill response plans, and first-aid procedures after any hazardous substance change.
Track Incident and Near-Miss Reports
Use them to spot weaknesses in your change management system and improve it.
Final Thoughts
Managing hazardous substances safely is a non-negotiable responsibility for every workplace. Yet, when changes occur — new chemicals, altered processes, or reorganized storage — risks can multiply quickly if not properly controlled.